How-to Articles
How-to choose protective film or tape
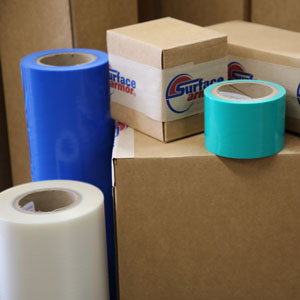
Samples for your application
Request a quote or free sample
Call us
888.753.3037
How to Choose Protective Film or Tape
The checklist that follows is a rough guideline that can be used to help you zero in on the optimum protective film for your particular application. You will probably want to evaluate two or three different films to find the best performer for your requirements. The more specifically you can identify the requirements of your application, the closer you can come to finding that perfect film the first time around.
How to Choose Protective Film or Tape. Also view our types of protective film page for even more information.
1. Identify the requirements for the ADHESIVE.
A. What surface is to be protected?
Metal type: ________________
Plastic type: ________________
Glass: ________________
High pressure laminate: ________________
Stone, marble, granite: ________________
Carpeting: ________________
Painted surface (fully cured): ________________
Other: ________________
B. What is the texture of the surface?
Smooth/glossy: ________________
Matte/textured/embossed: ________________
Coated? If yes, with what: ________________
C. What environmental issues might affect the adhesive?
Prolonged exposure to Sunlight / UV lighting: ________________
Temperature extremes: ________________
High positive pressure (such as the bottom unit of a tall stack): ________________
High negative pressure (wind or something pulling the away from the surface): ________________
High humidity: ________________
Moisture/rain/immersion: ________________
Chemical interaction with elements in the protected surface: ________________
Chemical interaction with elements in the environment: ________________
D. How long must the surface be protected?
Days ___ Weeks ___ Months ___
More than 6 months ___ More than a year ___
2. Identify the performance requirements for the protective FILM.
A. What does the film need to protect the surface from?
Abrasion:___ Staining:____
Scratching: ___ Etching: ___
Chipping: ___ Contamination: ___(over-spray, finger prints, dust, etc.)
B. What other properties are required from the film? __________________________
Does the protected surface need to be visible through the film? Yes No
Does the film need to stretch during stamping, forming or bending? Yes No
Does the film need to cut cleanly in a die press? Yes No
Does the film need a color tint to signal its presence? Yes No
Does the film need to have optical grade clarity? Yes No
Does the film need to protect against ESD (electrostatic discharge)? Yes No
3. Identify the size and dimensions of the tape/film product.
Does the film need to be perforated or cut to a shape? ___ width ___ length
Does the film need to be supplied as sheets on a release liner? Yes No
Will the film be dispensed by __ hand, from __ a dispenser or __ an applicator?
What roll/sheet dimensions are required?
___ Width ___ Maximum roll weight
___ Length ___ Maximum roll outer diameter
4. Assess the risks: what could possibly go wrong? Which of these might apply?
Adhesive could permanently bond the film to the surface. ___
Adhesive could stain the surface (ghosts of bubbles/wrinkles in the film).__
Adhesive could leave a sticky residue on the surface.___
Adhesive could lose its bond with the surface and fall off.___
5. Calculate your ROI: Do the potential rewards outweigh the potential risks?
reduced or eliminated surface damage: ___
greater customer satisfaction: ___
reduced shipping costs for returned goods: ___
reduced material costs due to rework: ___
reduced labor and handling costs due to rework: ___
reduced inventory holding costs: ___
greater plant capacity thanks to less rework: ___
over-time costs less: ___
higher morale in the executive suite: ____
6. What are typical test/evaluation procedures? It stands to reason that the greater the potential risk of damage that could be caused by a pressure sensitive adhesive, the more thorough the testing process should be. An ounce of prevention is worth a pound of cure − and all that − to prevent problems down the road.
A. Send sample films and the surface to be protected to a lab for a performance analysis.
- Wait 30 to 60 days for lab work to be performed and cross checked.
- Receive an inconclusive report with 3 pages of disclaimers and no recommendations.
- Receive a significant invoice for those inconclusive test results.
(The above scenario is meant to be somewhat tongue-in-cheek. Unfortunately, it can be a statement of fact. Before sending materials to a lab for analysis, ask the lab to indicate whether its report will include a recommendation or will it just be a list of findings.)
B. Perform an operational analysis of sample films on scrap stock.
- Apply sample film(s) to each target surface. Each paint/coating is a different surface. Each color is a different surface; dark colors show ghosting not seen on light colors.
- Place the surface in a vertical (up/down) position for initial adhesion testing.
- If the film immediately falls off, it probably won’t work for this application.
- If the film is still adhering to the surface, peel a portion of the film back.
- If the film pulls off very difficultly or tears when being removed, the tack may be
too high for your application. - If the film pulls the paint or other coating off of the surface the tack level is definitely too high for your application.
- If peeling the film off feels right, not too easily and not too difficultly, it is a candidate for further evaluation.
- If the film pulls off very difficultly or tears when being removed, the tack may be
- With the protected film surface standing vertically, wait 48 to 72 hours and perform the simple peel test again. (This is important because adhesives can become a bit more aggressive with the passing of time.)
- If the film passes this dwell-time test, consider the film for further testing.
- If the film falls off by itself or if it bonds far too tightly to the surface, it may not be a good candidate for your application.
Apply fresh samples to targeted surfaces and subject to probable usage environment and life cycle.
Why Surface Armor

Custom to You
The right film, adhesive, width, length, and perforation that fits. your exact needs

Quick Ship
Most orders ship within
2 days

Just in Time Quantities
You won't need to order a lifetime supply.
1,200 sq ft order minimums

Get FREE Samples Today
Contact us now and we will ship you a free sample to test